定价 380.00文章源自云智设计-https://www.cidrg.com/tao/9005.html
《现代完井工程(英文版)》论述了现代完井工程的新概念、新思路,并系统地提出了完井工程的定义、理论基础、工程内容和系统程序。是一本系统完整的完井工程专著。全书共分十一章。第一章主要叙述与完井工程相关的油田地质、油藏工程和采油工程等完井工程基础知识;第二章叙述了射孔完井、裸眼完井、衬管筛管完井三大类完井方式;第三章介绍了油管及生产套管尺寸的选定方法,现代完井工程的做法是先选油管一生产套管一技术套管一表层套管,阐述其理论根据;第四、五、六、七章叙述了完井液、射孔液、生产套管及注水泥射孔、完井的试井评价等方面的新技术和优化;第八章叙述投产前的各项预处理,如何解除油层伤害;第九章给出了常用的完井管柱,特别是给出了高压、高产油气井的管柱,还介绍国外完井管柱发展趋势;第十章重点讲述了高压高产、防腐蚀的井口装置;第十一章讲述了油气井腐蚀机理、防腐实例及防腐措施。文章源自云智设计-https://www.cidrg.com/tao/9005.html
编辑推荐
《现代完井工程(英文版)》可供从事油田钻井、采油、井下作业和油田开发设计技术人员应用,也可供石油院校教学参考。文章源自云智设计-https://www.cidrg.com/tao/9005.html
作者简介
万仁溥,Mr.Wan Renpu,a native of Nanchang,Jiangxi,China,was graduated from Petroleum Department of Tsinghua University in 1953.After that he worked in Shanbei,Yumen,Sichuan,Daqing and Shengli oil fields for 25 years.In 1978,he was transferred to the Development & Production Department of the Ministry of Petroleum Industry and later to the Development & Production Bureau of CNPC and appointed to be chief engineer and deputy director.He was engaged in drillingfor the first ten years and has been active in the production and research work in petroleum production engineering,workover treatment,well servicing operations and well completion engineering since.He has authored numerous technical papers in Chinese oil and gas journals and in JPT,World Oil and SPE,etc.and also authored more than ten books in petroleum production engineering and other readings in science &technology as well.Mr.Wan was awarded the titles of professor and specialist with outstanding contribution by the Ministry of Personnel of PRC in 1983 and 1989 respectively and enjoys the special allowance for specialist at state level.He is a chief founder in Chinese petroleum production engineering system.At present,he also is one of distinguished specialists in petroleum production engineering in China and a part-time professor of China Petroleum University,Southwestern Petroleum University,Xi'an Petroteum University and Jianghan Petroleum Institute.文章源自云智设计-https://www.cidrg.com/tao/9005.html
目录
INTRODUCTION
Basis of Well Completion Engineering
1.1 Grounds of Reservoir Geology and Reservoir Engineering
1.2 Core Analysis Techniques
1.3 Reservoir Sensitivity to Fluid and Working Fluid Damage Evaluation
1.4 Reservoir Stress Sensitivity Analysis
1.5 IN-SITU Stress and Mechanical Parameters of Rock
1.6 Technological Grounds of Petroleum Production Engineering
References
2 Well Completion Mode Selection
2.1 Vertical, Slant and Directional Well Completion
2.2 Horizontal Well Completion
2.3 Underbalanced Well Completion
2.4 Basic Requirements, Grounds and Flow Chart of Well Completion Mode Selection
References
Selection and Determination of Tubing and Production Casing Sizes
3.1 Overview
3.2 Overview of Nodal Analysis
3.3 Selection and Determination of Tubing and Production Casing Sizes for Flowing Wells
3.4 Selection and Determination of Tubing and Production Casing Sizes for Gas Wells
3.5 Selection and Determination of Tubing and Production Casing Sizes for Artificial Lift Wells
3.6 Effects of Stimulation on Tubing and Production Casing Size Selection
3.7 Selection and Determination of Tubing and Production Casing Sizes for Heavy Oil and High Pour-Point Oil Production Wells
References
4 Completion and Perforating Fluids
4.1 Functions of Drilling and Completion Fluid and Basic Requirements
4.2 Drilling and Completion Fluid Systems and Application
4.3 Shield-Type Temporary Plugging Technique
4.4 Drilling and Completion Fluid for Complicated Reservoir
4.5 Perforating Fluid
5 Production Casing and Cementing
5.1 Basic Requirements for Production Casing Design and Integrity Management of Production Casing
5.2 Hole Structure and Types of Casing
5.3 Strength of Casing and Strength Design of Casing String
5.4 Cementing
5.5 Production Casing and Cementing for Complex Type Wells
References
6 Perforating
6.1 Perforating Technology
6.2 Factors of Influencing Perforated Well Productivity
6.3 Perforating Differential Pressure Design
6.4 Optimizing Perforation Design
References
7 Well Completion Formation Damage Evaluation
7.1 Overview
7.2 Principle of Formation Damage Evaluation by Well Testing
7.3 Formation Damage Diagnosing in Homogeneous Reservoir by Graphic Characteristics
7.4 Graphic Characteristics of Dual Porosity Reservoirs and Reservoirs with Hydraulically Created Fracture
7.5 Distinction of Stimulation Effect by Graphic Characteristics
7.6 Quantitative Interpretation of Degree of Formation Damage
7.7 Well Logging Evaluation of Formation Damage Depth
References
8 Measures for Putting Well into Production
8.1 Preparations before Putting into Production
8.2 Main Measures for Putting into Production
8.3 Physical and Chemical Blocking Removal
8.4 Hydraulic Fracturing for Putting into Production
8.5 Acidizing for Putting into Production
8.6 High Energy Gas Fracturing for Putting into Production
8.7 Flowing Back
References
9 Well Completion Tubing String
9.1 Oil Well Completion Tubing String
9.2 Gas Well Completion Tubing String
9.3 Separate-Layer Water Injection String
9.4 Heavy Oil Production Tubing String
9.5 Completion Tubing String Safety System
9.6 Tubing String Mechanics
References
10 Wellhead Assembly
10.1 Oil-Well Christmas Tree and Tubinghead
10.2 Gas-Well Christmas Tree and Tubinghead
10.3 Water Injection and Thermal Production Wellhead Assembly
10.4 Common Components of Wellhead Assembly
References
11 Oil and Gas Well Corrosion and Corrosion Prevention
11.1 Related Calculation of Oil and Gas Well Corrosion
11.2 Oil and Gas Well Corrosion Mechanism and Classification
11.3 Material Selection for Corrosive Environment of Oil and Gas Wells
11.4 Oil and Gas Well Corrosion Prevention Design
11.5 Tubing and Casing Corrosion Prevention for Sour Gas Reservoir
References文章源自云智设计-https://www.cidrg.com/tao/9005.html 文章源自云智设计-https://www.cidrg.com/tao/9005.html
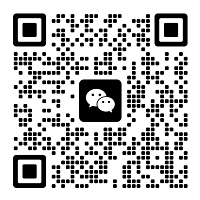
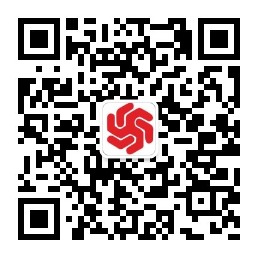