摘要: 高含硫天然气的安全高效净化处理对我国天然气工业发展具有重要意义。为此,在系统回顾我国含硫天然气净化技术的3 大发展历程的基础上,围绕天然气气质达标和硫磺回收装置尾气减排2 大难题,指出了脱硫脱碳、硫磺回收及尾气处理、净化装置稳定运行3 方面研究取得的进展、面临的挑战及攻关方向。研究结果表明:①以高含硫天然气有机硫脱除为核心的技术已开发成功并实现工业应用,可实现高含硫天然气达标净化处理,以CT-Redox 和CT-LOP 工艺为代表的络合铁法脱硫技术则有力地保障了我国高含硫天然气单井脱硫生产;②在现有常规与延伸克劳斯硫磺回收配套还原吸收与氧化吸收尾气处理技术基础上,研发的大型硫磺回收装置有机硫水解与尾气高效处理技术可满足日益严苛的国家标准要求,实现装置尾气超低排放;③以配方型脱硫胺液复活、高含硫净化厂设备腐蚀防护和净化装置长周期运行风险评价技术为代表的关键技术成效显著,有力地保障了净化装置的长周期安全平稳运行。结论认为,我国高含硫天然气净化技术已全面实现国产化,总体水平与国外相当,部分技术处于国际领先水平,建议在复杂含硫天然气中多组分有机硫深度脱除、净化装置尾气全天候全时段达标、物理化学类脱硫溶剂复活、高含硫净化厂耐腐蚀材质等方面开展技术攻关,以进一步提升我国高含硫天然气开发的技术水平。
关键词:高含硫;净化;脱硫;脱碳;硫磺回收;尾气处理;腐蚀;醇胺文章源自云智设计-https://www.cidrg.com/news/forward/20278.html
0 引言文章源自云智设计-https://www.cidrg.com/news/forward/20278.html
天然气是一种洁净、方便、高效的优质燃料,也是重要的化工原料。自20 世纪60 年代以来,随着国民经济高速发展以及对能源需求的大幅增长,中国天然气工业得到了快速发展。2022 年,世界天然气产量达40 160×108 m3,中国首次突破2 200×108 m3。作为一种清洁能源,等热值天然气的CO2 排放量比石油少25% ~ 30%,比煤炭少40% ~ 50%,是中国能源体系“碳减排”的重要抓手,将发挥着不可替代的作用[1]。文章源自云智设计-https://www.cidrg.com/news/forward/20278.html
美国、俄罗斯、中国和加拿大四大天然气主产国含硫天然气占比超过15%[2],天然气中所含剧毒H2S 是致命性气体,安全阈值为15 mg/m3,含硫天然气必须进行脱硫、脱碳和硫磺回收等净化处理,才能进行商业应用[3]。20 世纪60 年代以来中国天然气净化技术开始起步,历经了从无到有、从有到优的发展历程,取得了长足进展,推动了含硫天然气、特别是高含硫天然气工业飞速发展。“十四五”以来,以高效脱硫脱碳、超低排放硫磺回收及尾气处理、净化装置关键设备腐蚀控制及受污染溶液复活等为代表的高含硫天然气净化关键技术取得重大突破,助力了中国天然气高效生产与清洁替代。文章源自云智设计-https://www.cidrg.com/news/forward/20278.html
1 国内外高含硫天然气分布及开发现状文章源自云智设计-https://www.cidrg.com/news/forward/20278.html
《天然气藏分类:GB/T 26979—2011》[4] 规定,H2S含量超过2%(30 g/m3)以上为高含硫天然气。全球高含硫气藏资源丰富,主要分布在加拿大、美国、法国、俄罗斯和中国等地。国外主要高含硫气田概况如表1 所示。文章源自云智设计-https://www.cidrg.com/news/forward/20278.html
表1 国外高含硫气田概况表文章源自云智设计-https://www.cidrg.com/news/forward/20278.html
文章源自云智设计-https://www.cidrg.com/news/forward/20278.html
加拿大是高含H2S 气田较多的国家,其储量占全国天然气总储量的1/3 左右,主要分布在落基山脉以东的内陆台地。俄罗斯已探明油气田中,20% 以上为高含硫,储量近50 000×108 m3,主要集中在阿斯特拉罕凝析气田和奥伦堡凝析气田。文章源自云智设计-https://www.cidrg.com/news/forward/20278.html
中国高含硫天然气累计探明储量已超1×1012 m3,其中90% 以上位于四川盆地。20 世纪60 年代以来,继成功开发了四川盆地的威远震旦系、卧龙河、中坝雷三段等高含硫气藏后,又陆续成功开发了龙岗、罗家寨、普光、元坝以及海外阿姆河等大型高含硫气藏。中国主要高含硫气田概况如表2 所示。文章源自云智设计-https://www.cidrg.com/news/forward/20278.html
表2 中国高含硫气田概况表
2022 年,四川盆地超1/4 产量来自高含硫气藏。已建成的高含硫气田主要有:中国石化普光气田、中国石油罗家寨气田、中国石化元坝气田;近期,中国石油铁山坡气田已经建成投产,渡口河气田也进入加快建设阶段。
2 天然气净化技术发展历程
天然气净化技术的发展总体要适应于天然气勘探开发技术的发展,并受天然气气质标准和大气污染物排放标准驱动。随着中国天然气产量与两大标准要求的不断提高,不断催生出新技术。相关的气质标准和大气污染物排放标准历次制修订情况如表3 所示。
表3 两项标准制修订情况表
从表3 可见,天然气气质标准总硫含量历经100 ~ 60 ~ 20 mg/m3 的逐级递减,大气污染物排放标准SO2 排放浓度则历经960 ~ 400 mg/m3 的逐级递减。中国天然气净化技术的发展,也与标准制修订息息相关,大致可分为3 个阶段[5]。
2.1 天然气净化技术起步阶段
20 世纪60—70 年代为天然气净化起步阶段。此阶段中国天然气净化技术主要以跟踪学习国外技术为主,实现了天然气净化工业零的突破。国外20 世纪40 年代开始天然气净化技术研究,1957 年加拿大建成世界第一套单乙醇胺(MEA)脱硫和克劳斯硫磺回收装置。
20 世纪60 年代以前,国内天然气生产规模很小,主要采用碱液法和砷碱法工艺进行脱硫净化处理。20世纪60 年代以来,中国天然气生产逐渐实现工业化与规模化。1965 年,第一套单乙醇胺法天然气净化工艺在东溪净化厂建成投产,迈出了天然气净化工业化的第一步。20 世纪70 年代,成功开发了环丁砜和一乙醇胺混合脱硫溶液。70 年代末,成套引进了当时具有国际先进水平的Sulfinol-D 脱硫工艺。通过对引进技术的消化吸收,丰富了川渝地区天然气净化工艺技术水平。同时,采用二级和三级克劳斯工艺回收脱硫再生酸气中的硫磺,先后建成威远脱硫一厂、威远脱硫二厂和卧龙河脱硫厂。
2.2 天然气净化技术发展阶段
20 世纪80 年代至2015 年为天然气净化技术发展阶段。此阶段中国天然气净化技术在消化吸收国外技术的基础上有了长足进步,实现了常规天然气净化技术的全面国产化。20 世纪80 年代以来,国外开发了配方型溶剂脱硫和延伸克劳斯技术,进一步提升了天然气净化技术水平。中国研发的具有明显节能效果的甲基二乙醇胺(MDEA)选择性脱硫工艺实现了工业化,初步建立了天然气脱硫技术体系。通过引进CBA、MCRC、SuperClaus 等硫磺回收新工艺解决了制硫关键技术难题。该期间,中国自主开发了选择性脱硫、脱硫脱碳、有机硫脱除等系列技术,自行开发了CPS 和国产直接氧化工艺,先后建成了中国石油长庆1-5 天然气净化厂(以下简称净化厂)、塔里木塔中1-3 联合站、忠县净化厂、川西北净化厂等。中国石化普光净化厂和元坝天净化厂等一批高含硫净化厂也相继建成投产。净化厂各项技术经济指标和安全环保指标均满足了当时的天然气气质标准和大气污染物排放标准,并已进入世界先进水平行列。
2.3 天然气净化技术深化阶段
2015 年至今为天然气净化技术深化阶段。此阶段中国天然气净化技术发展迅速,通过新工艺新技术研发,实现了对部分国外技术的超越。为满足天然气气质标准和大气污染物排放标准,中国对原料天然气中有机硫脱除和大型硫磺回收装置尾气处理技术开展了多轮攻关。有机硫脱除技术方面,通过提高溶剂与有机硫的化学反应速率,同时提升物理吸收性能,开发了高效脱除羰基硫(COS)和硫醇(RSH)的溶剂法有机硫脱除技术。还开发了天然气COS 水解技术,通过固定床催化反应,有效转化原料气中的有机硫。尾气处理技术方面,则开发了低温加氢技术、SO2 选择性吸收技术和SO2 催化吸附工艺。先后建成中国石油宣汉、剑阁、安岳等高含硫净化厂和遂宁、苍溪一、大庆徐深9 等中低含硫净化厂。渡口河高含硫净化厂即将建成投产,安岳南区和大英北区等净化厂正在筹建中。
3 高含硫天然气净化技术进展
“十三五”以来,随着中国高含硫气藏的持续上产、国家对环保要求日益提高,高含硫天然气净化技术不断发展完善,在脱硫脱碳、硫磺回收及尾气处理、净化装置稳定运行等方面取得了新的进展,推动了国内天然气净化技术的不断深化。
3.1 脱硫脱碳技术
根据原料气气质条件和净化需求不同,可分为高碳硫比天然气选择性脱硫、高含硫高含CO2 天然气脱硫脱碳、高含硫天然气有机硫脱除和高含硫天然气单井脱硫4 类技术。
3.1.1 高碳硫比天然气选择性脱硫技术
对于高碳硫比天然气,因其脱硫脱碳后酸气中的H2S 含量低,不利于硫磺回收装置操作,因此,必须考虑溶剂的选择性。利用脱硫溶剂的选择性,在保证H2S 净化度的前提下,尽可能减少对CO2 的脱除,以改善酸气质量[6]。当前国内外在高碳硫比天然气脱硫中研究及应用较多的为MDEA 脱硫技术。MDEA为叔胺,其分子结构中无活泼氢原子,与CO2 仅能进行生成碳酸氢盐的慢反应,属于液膜控制过程[7]。
针对在高碳硫比气质条件下选择性脱除H2S 的技术难题,中国石油自主研发了抑制CO2 吸收速率的活性添加剂,通过抑制剂降低溶剂体系与CO2 的反应速率,一方面提高了酸气浓度,另一方面降低了再生所需蒸汽耗量,对CO2 的共吸率较MDEA 降低了5% ~ 10%,目前在遂宁净化厂、忠县净化厂、磨溪净化厂等工业应用。其次,自主研发了空间位阻胺选择性脱硫技术。空间位阻胺是指氨基(H2N-)上的一个或两个氢原子被体积较大的烷基或其他基团取代后形成的胺类[8]。这些大基团的引入,使醇胺分子具有了显著的空间位阻效应,限制了其与CO2 的反应,同时保留了与H2S 反应的良好活性[9]。中国石油近年来开展了对空间位阻胺的系统研究,结合位阻基团种类、个数和位置的设计,并在分子结构中引入了羟基、氨基和乙氧基等特殊基团,设计出适用于选择性脱硫的新型空间位阻胺分子结构,并在最优条件下实现了自主合成空间位阻胺,其对CO2的共吸率较MDEA 降低了13%,可实现对H2S 的高效脱除,达到了国际先进水平。
3.1.2 高含硫高含CO2 天然气脱硫脱碳技术
对于H2S 和CO2 含量皆较高的天然气,采用选择性脱硫技术无法使净化气达到管输要求,需将净化气中CO2 脱除到较低水平以满足下游化工要求时,需要采用脱硫脱碳技术。针对高含硫高含CO2 的天然气,国内外常用的脱硫脱碳溶剂主要是以MDEA为主剂,配合MEA、DEA 或哌嗪等组分使用[10]。常规脱硫脱碳溶剂在原料气中CO2 分压较低且有氧存在的情况下,存在再生能耗较高和溶剂降解损耗大等缺点。
针对上述问题,中国石油基于对CO2 的脱除机理研究,从胺分子结构、反应速率、化学焓等基础物性入手,结合醇胺法工艺的主要能耗环节分析,自主研发了具有高吸收性能、较低再生能耗的混合胺脱硫脱碳技术和活化MDEA 脱碳技术,并已工业应用[11]。其中混合胺脱硫脱碳技术通过叔胺与伯仲胺配伍可以提高低压下的H2S 净化度,亦能确保CO2小于3% 或CO2 脱除率大于90% 的净化要求;活化MDEA 脱碳技术通过引入多胺和两性离子活化剂进一步加强溶剂组分之间的传质效应,并有效抑制氧化降解速率。CO2 可以脱除至50 mg/m3 以下,再生能耗小于2.7 GJ/t CO2,溶剂损耗小于0.5 kg/t CO2,达到国外先进脱碳溶剂水平。
3.1.3 高含硫天然气有机硫脱除技术
对于原料气中有机硫含量较高(大于30 mg/m3)的气质,需使用有机硫脱除技术实现气质达标。中国高含硫中有机硫主要以COS 和RSH 为主[12]。目前国内外针对天然气中有机硫脱除主要采用物理—化学溶剂法,该法兼具物理溶剂法和化学溶剂法的优势和特点,主要由环丁砜、醇胺和水等组成[13]。国外应用较广的物理—化学溶剂有壳牌公司的Sulfinol-M和Sulfinol-X 以及陶氏化学Ucarsol Hybrid 920。
针对有机硫酸性弱、分压低,难以深度脱除的难题,中国石油基于对COS 和RSH 的脱除机理研究,通过醇胺分子结构改进,促进有机硫在溶液中离解,提升了有机硫的脱除效果,自主开发了选吸型有机硫脱除技术和全脱型有机硫脱除技术。选吸型有机硫脱除技术可大部分脱除有机硫,保留部分CO2,中国石油技术与壳牌Sulfinol-M 相比,总有机硫脱除率提高约10%。全脱型有机硫脱除技术可基本完全脱除天然气中的酸性组分,中国石油技术与壳牌Sulfinol-X相比,大幅提升了RSH 的脱除效果。国内外选吸型有机硫脱除技术和全脱型有机硫脱除技术应用情况如表4 和表5 所示。
表4 国内外选吸型有机硫脱除技术应用效果表
表5 国内外全脱型有机硫脱除技术应用效果表
针对COS 与CO2 分子结构相近,但COS 酸性更弱,溶剂在大量脱除COS 时CO2 基本全部脱除,造成溶液酸气负荷较高、循环量大、再生酸气H2S浓度低、商品气损失大等问题[14],中国石油自主开发出COS 水解技术,研发了COS 水解催化剂,形成了工业包。该技术适用于COS 含量较高(大于100 mg/m3)的原料气,在主吸收塔后端增加COS 水解装置,在催化条件下将原料天然气中COS 水解转化为H2S 和CO2,达到深度脱除COS 的目的。该技术在万州净化厂工业应用,COS 水解率大于99%,水解反应温度比国外同类产品降低40 ℃,每年可节约燃料气约160×104 m3,技术水平国际领先。
3.1.4 高含硫单井脱硫技术
对于含硫单井天然气,需要采用投资成本低、建设周期短、H2S 脱除效果好的单井脱硫技术,以满足含硫天然气单井产能有效发挥的需求。以络合铁法为主的单井脱硫技术针对含硫单井天然气处理规模不大、潜硫量不高(0.2 ~ 20.0 t/d)的特点,在实现含硫天然气高效净化的同时实现硫磺回收的功能,在含硫天然气单井试采与边远分散气井产能发挥中展现出较高的适应性和经济性。该类技术主要包括络合铁法脱硫与生物脱硫。
络合铁法脱硫技术使用具有兼顾络合性能与抗氧化性的多氨基多羧酸盐作为络合剂,在pH 值介于7 ~ 9 条件下维持铁/ 亚铁离子浓度与循环,实现对H2S 的反应脱除与硫磺回收[15]。基于络合铁法脱硫技术原理,国外形成了LO-CAT、SulFerox、Sulfint HP 等络合铁法脱硫工艺,其中应用最广泛的LO-CAT 工艺在全球拥有230 余套装置。通过对LO-CAT 工艺技术的引进、吸收与创新,国内络合铁法脱硫技术迅速发展,中国石油开发了CT- Redox与CT-LOP 工艺,中国石化开发了MCS 工艺,并达到国际先进水平。针对络合铁法脱硫技术存在稳定运行硫化氢容量不高以及硫磺颗粒分布规律、沉降状态认识不清的问题,中国石油通过对络合铁溶液关键组分络合剂、表面活性剂构效关系研究[16],对络合体系稳定性和硫磺颗粒尺寸分布进行有效控制,开发的CT- Redox 工艺H2S 容量可达1.0 g/L 以上,适应潜硫量可达20 t/d。络合铁法脱离技术典型案例如表6 所示。
表6 国内天然气络合铁脱硫技术应用案例表
天然气生物脱硫技术利用特殊微生物酶Fcc 和酶Sqr 的生化作用,将硫化物转化为单质硫或硫酸盐。生物脱硫的技术优势主要在两方面:①生物硫磺表面多聚硫化物和多聚有机物组成的复合带电层提高了硫磺颗粒亲水性,硫磺粒径约15 μm,沉降速率约7 mm/s,降低设备堵塞风险;②微生物代谢作用对有机硫有一定的脱除能力。但相关研究表明有机硫,尤其是CH4S 会引起微生物细胞分解、抑制生物氧化特性、诱导生成疏水性硫磺等。生物脱硫在工程应用中面临过程控制精细、条件要求苛刻等问题,溶液pH 值、供氧量的波动会显著影响副盐生成率,导致较大量的废水排放。通过生物菌种筛选驯化与生物反应器设计控制反应进度可提高单质硫的形成率和选择性,从而避免过氧化生成硫酸盐和硫代硫酸盐造成废水排放。目前以Shell-Paques/Thiopaq 为代表的生物脱硫技术已成熟应用于中低潜硫量的气体液相脱硫及硫磺回收过程,在大型规模化天然气脱硫领域应用较少[17]。中国石油于 2009 年开始了天然气生物脱硫技术研究,重点进行了脱硫菌种的筛选和改良、溶液体系的开发、工艺过程设计与优化等相关研究工作,并取得了良好的研究成果,逐步走向工业试验[18]。含硫天然气生物脱硫技术典型案例如表7 所示。
表7 含硫天然气生物脱硫技术应用与研究案例表
3.2 硫磺回收及尾气处理技术
净化厂脱硫脱碳后副产酸性气普遍采用以克劳斯技术为核心的硫磺回收工艺。为进一步降低环境污染,采用加氢还原和氧化吸收处理尾气,以满足日益严苛的尾气排放标准。国内硫磺回收及尾气处理技术总体已达国际先进水平。
3.2.1 常规克劳斯技术
常规克劳斯硫磺回收工艺通过H2S 部分燃烧,再进行二级或三级催化转化实现硫磺回收。常用活性氧化铝作为催化剂,其对克劳斯反应具有良好的催化转化效果[19]。
针对常规克劳斯工艺过程气组成比较复杂,含5 000 ~ 20 000 mg/m3 有机硫(COS 和CS2)和500 ~10 000 mg/m3 氧,导致装置总硫回收率下降,催化剂使用寿命变短问题,以钛基有机硫水解催化剂和脱氧型氧化铝催化剂为核心,国内外均研发了克劳斯有机硫水解和抗氧技术。在有机硫水解技术方面,美国Axens 公司、中国石油和中国石化所开发的技术具有催化剂纯度高和耐水热性能好的特点。抗氧技术方面,则以中国石油和中国石化技术为主。二者均可在最高5 000 mg/m3 漏氧情况下维持稳定的克劳斯转化率。国内外克劳斯有机硫水解与抗氧技术主要指标对比如表8 所示。
表8 国内外克劳斯有机硫水解与抗氧技术主要指标对比表
有机硫水解技术与抗氧技术通常组合应用,以发挥装置最大功效。中国石油技术在安岳净化公司和中国石化技术在元坝净化厂的工业应用效果如表9 所示。
表9 中国石油与中国石化技术应用效果表
3.2.2 延伸克劳斯技术
20 世纪80 年代,为提升效率,开发了以低温克劳斯和H2S 选择性氧化工艺为代表的延伸克劳斯技术。低温克劳斯工艺在低于硫露点的温度下进行克劳斯反应,可突破硫露点对操作温度的限制;H2S 选择性氧化工艺则以不可逆的H2S 部分氧化为硫磺的反应替代可逆的克劳斯反应,将单级反应器硫转化率从50% ~ 70% 提高到85% 左右[20]。典型的低温克劳斯工艺有:美国的CBA、加拿大MCRC 和中国石油的CPS 工艺。H2S 选择性氧化工艺主要是荷兰的SuperClaus 工艺,中国石油将其国产化后形成了国产直接氧化(SCO)工艺。
针对普通活性氧化铝催化剂应用于低温克劳斯工艺条件下易发生硫沉积导致失活的问题,中国石油通过研发特殊添加剂,实现了对氧化铝孔结构的调控,开发了高比表面大孔活性氧化铝催化剂,实现了对液硫产物的高容量吸附。针对SuperClaus 工艺用硅基催化剂不易成型,强度较差问题,通过调配超细二氧化硅原料结构,成功制备出高强度硅基催化剂,实现了特殊克劳斯工艺用催化剂的国产化。美国、荷兰、中国石油和中国石化催化剂情况如表10 所示。
表10 延伸克劳斯工艺催化剂情况表
3.2.3 还原吸收尾气处理技术
还原吸收尾气处理技术最早由荷兰壳牌公司开发。通过加氢段将尾气中绝大部分非H2S 硫化物转化为H2S,再吸收再生返回克劳斯装置处理。加氢反应器所用催化剂决定了加氢段能耗与性能。典型的还原吸收尾气处理技术有:国外SCOT、RAR 和CR工艺;中国石油CPH 工艺。SCOT 工艺是目前应用最广泛的工艺,在国内应用厂家超过50 家。还原吸收尾气处理工艺主要情况如表11 所示。
表11 还原吸收尾气处理技术主要情况表
针对低温还原吸收尾气处理工艺中常规钴钼催化剂活性下降,有机硫水解不彻底的问题,采用三元金属浸渍技术,以稀土金属改性催化剂,实现了低温下有机硫的高效水解。法国Axens 公司、荷兰壳牌公司、中国石油均开发了相应的低温加氢水解技术,具体情况如表12 所示。
表12 国内外低温加氢水解技术对比情况表
3.2.4 氧化吸收尾气处理技术
氧化吸收尾气处理技术是将克劳斯尾气中的各种含硫化合物高温焚烧为SO2,再通过有机胺对尾气中的SO2 进行脱除,以提高总硫回收率。最具代表性的是Cansolv 工艺,其可将排放尾气中的SO2 浓度降低至50 mg/m3 以下,实现超低排放。但尚存在含盐污水排放量大和文丘里急冷塔腐蚀严重等问题。Cansolv 工艺流程如图1 所示。全球目前有超过25套装置在运行,典型应用厂家为中国石油安岳净化公司、忠县净化厂、苍溪净化一厂。
图1 Cansolv 工艺流程图
针对氧化吸收工艺用有机胺的国产化问题,中国石油首次建立了SO2 和CO2 各吸收形式的分布模型,在此基础上开发了一种可实现高气液比、高稳定、高选择、可再生及深度脱除SO2 的有机胺脱硫溶剂。与进口壳牌公司DS 溶剂相比,二者均能将SO2 脱除至小于50 mg/m³ 的程度,而国产溶剂对SO2 的脱除深度优于进口溶剂。在循环80 h 后,国产溶剂尾气SO2 含量为11.3 mg/m3,进口溶剂为31.2 mg/m3。
3.3 高含硫净化装置稳定运行技术
保证净化装置平稳操作的要点可归纳为3 方面:①保持醇胺脱硫脱碳溶液(以下简称胺液)性能良好。对受污染胺液进行复活以恢复其性能,这是保障胺液性能良好的关键;②防止设备腐蚀,研究以设备设施腐蚀监测、腐蚀预测预防为主的净化装置腐蚀控制技术是装置安全运行的重要手段;③科学制订检维修计划。
3.3.1 胺液复活技术
胺液在净化天然气过程中会变质,造成净化装置腐蚀、脱硫性能下降、运行不平稳、发泡严重时被迫停产[21-24]。随着天然气上产步伐不断加快,胺液变质问题对生产的影响比过去更为突出,严重制约了净化生产环节的稳定和上产。以转化和脱除胺液中有害变质产物,恢复胺液性能为目的开发的胺液复活技术是保障净化装置稳定高效运行的关键技术手段。
国内外已有加碱处理、常压蒸馏、减压蒸馏、活性炭吸附、离子交换、电渗析[25-28] 等复活技术,其对最影响净化装置稳定运行的致泡性变质产物脱除率很低,即使最先进的美国、加拿大胺液复活技术,对致泡性变质产物的脱除率也低于20%,无法解决胺液变质发泡导致的装置波动、处理量降低、停产等生产难题。胺液中的致泡性变质产物大部分沸点都比醇胺高,理论上可以采用蒸馏的方法分离去除,但实际效果不佳,因为含有致泡性变质产物的胺液沸腾时会起泡,致泡性变质产物聚集在泡沫表面而被醇胺带走。针对胺液中致泡性变质产物种类多、性质差异大、难以全部脱除且脱除深度要求高的难题,国内外没有成功经验可借鉴。中国石油原创开发了致泡性变质产物脱除剂与工艺。在充分研究各种致泡性变质产物分子连接性指数、特征官能团、化学反应活性等物化特性的基础上设计吸附剂,从极化率、表面电荷、孔穴结构、特异性功能基、活性组分等方面强化吸附剂与致泡性变质产物分子的相互作用势能,设计固定床吸附—再生工艺流程。通过物理和特异性化学吸附作用实现了对胺液中70 余种致泡性变质产物的深度脱除,脱除率超过97%。在遂宁净化公司、苍溪净化一厂、剑阁、引进、磨溪等净化厂的应用表明,即使消泡时间高达3 600 s 以上发泡非常严重的胺液,复活后起泡趋势也恢复到了与新鲜胺液相当的水平,首次成功攻克了胺液变质发泡的难题(表13)。
表13 净化厂变质胺液复活前、后发泡性能对比表
国内外已有胺液复活技术脱除腐蚀性变质产物——热稳定盐时,会同时脱除配方型醇胺溶液中加强H2S 选吸性的活性添加剂。所以,已有技术解决了热稳定盐导致的腐蚀问题,但又造成胺液脱硫性能严重下降,天然气净化厂处理量大幅降低的问题。针对配方型醇胺溶液在复活过程中活性添加剂与热稳定盐共脱除的难题,中国石油发明了一种含排斥基的新型金属有机配位分离材料,在此基础上形成的热稳定盐选择性脱除技术,在热稳定盐脱除率不降低的前提下对活性添加剂的保留率比已有技术提高了96.5%。针对国内外离子交换胺液复活技术脱除无机热稳定盐时会生成无机碱,导致胺液中的硫氢根浓度增大,继而使醇胺吸收H2S 的化学平衡逆向移动,造成胺液脱硫性能下降的难题,中国石油发明了无机热稳定盐转化技术,引入带亲电基团的聚合物吸附醇胺分子使其质子化,再与无机热稳定盐反应,使其定向转化为热稳定胺盐(其复活产物是醇胺和水),避免了无机碱的生成。热稳定盐选择脱除技术和无机热稳定盐转化技术在宣汉、安岳净化公司、遂宁净化公司、苍溪净化一厂、引进、磨溪、剑阁等净化厂的13 套净化装置的应用表明,这两项技术不仅降低了胺液腐蚀性,还恢复了胺液的脱硫性能(表14)。解决了胺液变质后脱硫性能无法恢复这个长期困扰含硫天然气净化行业的共性难题。
表14 净化厂变质胺液复活前、后脱硫性能对比表
在致泡性变质产物脱除、热稳定盐选择性脱除、无机热稳定盐转化3 项技术的基础上集成开发了胺液深度复活工艺。胺液深度复活工艺是目前国内外唯一一种能深度脱除醇胺溶液中70 余种致泡性变质产物,热稳定盐脱除率和活性添加剂保留率均能达到大于90% 的技术(表15)。在胺液复活技术领域实现了从“跟跑”到“领跑”的跨越式发展。
表15 胺液复活技术对比表
3.3.2 净化装置腐蚀控制技术
高含硫净化装置工艺节点多、规模大,运行工况涉及高温、高压、高酸气、热稳定盐,且气、液、固三相交互耦合,导致净化装置腐蚀失效时有发生,影响净化装置的长周期平稳运行。国内外研究普遍从腐蚀薄弱环节、腐蚀主控因素研究出发,目前已经形成基本满足石化行业标准要求的净化厂腐蚀控制技术,结合腐蚀监/ 检测体系,可有效管控净化厂装置安全运行。
针对净化厂腐蚀因子多,控制因素识别难的问题,国内外学者通过室内试验模拟评价、现场腐蚀监/ 检测、失效案例分析,明确了净化厂腐蚀易发生部位主要集中在腐蚀环境涉及高温、酸气、酸水的设备与管线,如再生塔、重沸器及再生环节的碳钢管线,并相继开展了酸气(H2S/CO2)、Cl -、热稳定性盐、温度、流速等因素对不同设备材质的腐蚀行为研究[29]。通过引入灰色关联度法,进一步明确了净化装置的腐蚀主控因素及其占比(图2),并首次发现了甘氨酸对腐蚀的影响(图3)。
图2 基于灰色关联的腐蚀主控因素及其占比图
图3 甘氨酸含量对腐蚀速率的影响图
鉴于主控因素研究结果,国内外普遍从工艺参数控制、合理选材及结构优化3 个方面开展研究[30],并形成三位一体的综合防控技术。如普遍要求碳钢设备酸气负荷低于0.6 mol/mol,胺液流速低于1.0 m/s,胺液浓度低于50%,醇胺溶液再生塔小于127 ℃。针对需要重点关注,且国外研究较少的热稳定性盐控制指标[31],中国石油通过系统研究,给出了详细的热稳定盐控制值(表16)。对于频繁出现腐蚀失效及泄漏后果较高的设备建议优化结构及升级管材,从设计上保障设备和管线的本质安全[32]。加拿大Brazeau净化厂再生塔、重沸器等设备采用了不锈钢或复合钢板材质。中国石化普光净化厂、中国石油宣汉和万州净化厂设备的选材如表17 所示。此外,国外对缓蚀剂控制技术也有研究,但普遍应用于净化厂循环水系统。中国石油针对常规循环水缓蚀阻垢剂含磷量高,不适应环保要求的问题,基于多元协同作用,研发形成一种具备晶格畸变作用的聚羧酸型无磷缓蚀阻垢剂,可将循环水的总磷含量控制低于0.5 mg/L,腐蚀速率不大于0.075 mm/a,阻垢率不低于90%,国内外性能指标对比如图4 所示。
表16 热稳定盐控制指标表
表17 高含硫净化厂设备材料表
图4 无磷缓蚀阻垢剂性能对比图
腐蚀监/ 检测方面,国内外普遍采用多种监/ 检测技术联合使用,为运行管理提供决策依据[33],技术难点主要在于监/ 检测点的选择如何兼具经济性及代表性。监/ 检测重点通常为脱硫单元、尾气处理单元、硫磺回收单元中的换热器、塔器、罐类、管线弯头等。腐蚀监测常用方法包括:挂片法、电感探针法、电阻探针法、线性极化法、电化学噪声技术、超声波测厚腐蚀监测法等,优先采用挂片法+ 电感/ 电阻探针法,对于焊缝处、管线弯头等位置推荐使用固定式超声波腐蚀监测法,其他方法可作为装置出现严重腐蚀问题时的补充。宣汉净化厂建立较为完整的腐蚀监测体系,结合工艺流程与腐蚀机理,确定腐蚀监测部位,分别采用腐蚀挂片、定点测厚、射线剖面成像、管道外部漏磁等多种腐蚀监控手段。以脱硫系统为例,设备测厚如图5 所示,结果显示除脱硫系统再生塔中下局部点位最大减薄量超过10% 外,其余设备整体处于轻度减薄(壁厚减薄小于10%)。
图5 脱硫系统再生塔超声波测厚图
无损腐蚀检测技术主要有超声检测、相控阵、衍射时差法超声检测、电磁超声检测、涡流检测等,并逐渐向智能化、功能多样性以及信息中国石油开放化方向发展,实际应用中应依据设备结构特点、运行工况选择相应的检测技术组合以优势互补[34]。现场多采用“目视+ 渗透+ 超声测厚”的组合方式,发现疑似缺陷,再精检复验。现阶段国内外净化装置的腐蚀检测均是在停产检修阶段,为了满足净化装置长期安全运行迫切需要,及时发现运行阶段不可预见和无法监测到的腐蚀问题,已在国内率先开展了净化装置不停车在线腐蚀检测技术可行性实践,克服了运行条件下面临的高空、高温、动火等作业安全风险以及检测精度降低的难题,综合采用高温电磁超声、脉冲涡流、阵列涡流、DR 射线等技术手段,对分离器、吸收塔、再生塔等塔罐和管线进行了不停车检测,创新形成不停车在线腐蚀检测总体技术思路,如图6所示,为检修周期决策提供了重要支撑。
图6 不停车在线腐蚀检测技术思路图3.3.3 净化装置长周期运行风险评价技术
针对净化装置每年开展停产检修的现状,延长检修周期的决策难点在于科学识别限制装置长周期安全运行的风险。通过开展长周期运行风险评价技术研究,形成了基于完整性评价的综合评价技术,并在多套净化装置开展应用。在中石化所属普光天然气净化厂和元坝天然气净化厂通过多列装置轮修实现了“三年一修”,在中石油所属单列装置天然气净化厂大部分实现了“两年一修”。近年来,开发了净化厂多种风险评价技术,其中RBI、RCM 和HAZOP/LOPA/SIL 联合评价技术应用效果好,应用较广泛。
RBI(Risk-Based Inspection,基于风险的检验)技术是以设备的风险分析及风险分布为基础,制定合理的检验计划,延长低风险设备的检验周期,确保设备安全运行的基础上提高经济效益;RCM(Reliability-Centered Maintenance,以可靠性为中心的维修)技术通过系统地对装置中设备的失效模式及后果进行分析和评估,定量评价每个失效模式的风险及失效原因,并制订出针对维护策略,是目前国际上流行的、用以确定设备预防性维修工作、优化维修制度的一种系统工程方法;HAZOP(Hazard andOperability,危险与可操作性风险分析)是一种定性分析危险性的评价方法,用于探明生产装置和工艺过程中的危险及其原因,寻求削减对策;LOPA(Layerof Protection Analysis,保护层分析)是一种半定量的工艺危害分析方法,用于确定发现的危险场景的危险程度,定量计算危害发生的概率,对已有保护层的保护能力不足的可以推算出需要的保护措施;SIL(Safety Integrity Level,安全完整性等级)是一种定量的安全评价方法,针对安全仪表系统的一些关键因素如安全失效分数、平均失效概率等进行计算,得到设计合理的SIL 等级。
4 天然气净化技术面临的挑战及发展趋势
随着中国高含硫天然气开发不断向超深、超高温、复杂碳酸盐岩储层进军,勘探开发对象日趋复杂,高含硫天然气资源品质劣质化趋势不断加剧。高含硫、高含碳、高含有机硫天然气的净化处理将成为常态。这对中国高含硫天然气净化提出了4 大挑战。针对这4 大挑战,建议开展相应的技术攻关,作好技术储备。
4.1 天然气净化技术面临的挑战
1)安全环保要求方面。商品天然气质量和天然气净化厂外排尾气SO2 浓度控制越来越严格,给高含硫天然气净化技术提出了更高的要求,体现在两方面:① GB 17820 和GB 39728 两大标准可能参照汽柴油产品标准和炼油厂尾气排放标准进一步收紧,天然气净化厂尾气全天候全时段达标工作已开始部署,天然气净化厂现有脱硫和硫磺回收技术需要不断升级;②净化装置性能下降对生产的影响进一步增大,净化装置性能小幅度的下降都可能造成产品气和尾气超标,或产量降低,净化装置性能监控技术的精准性、时效性与效率需要进一步提高。
2)生产保障方面。在能源结构优化、保障能源安全的背景下,含硫天然气开发速度将不断加快,硫化物深度脱除与高效转化技术是实现油气清洁生产的重要保障,并需要净化厂进一步提高稳定运行周期,实现产量增长,提高保供能力。随着勘探开发向超深层挺进,天然气净化面临原料气气质中有机硫含量增加及种类愈加复杂,对有机硫脱除技术提出了更高要求;同时随着钻完井、储层改造、排水采气、集输系统防腐等各环节新技术与新工艺的应用,原料天然气携带杂质情况发生变化且更为复杂,加大了净化装置稳定运行的难度。体现在两方面:① 复杂含硫气中硫化物精准脱除难度大,现有技术在商品气脱损、装置运行能耗等方面还需进一步优化;②开发技术变化后带来的原料天然气杂质组成变化对净化装置运行的影响尚不明确,相应的对策技术研发缺乏依据,难以找准方向。
3)新技术发展方面。光学、电学、材料、计算机、电子信息等领域技术发展迅速,如何应用这些领域的新研究成果,推动高含硫天然气净化装置稳定运行保障技术向着更精准、环保、高效、智能化方向发展,尚需开展大量的探索性研究。
4)适应新的生产需求方面。随着勘探开发深入,超深、高含硫、大产量探井及评价井不断出现,尽早实现这类井单井试采,气藏高效开发急需解决的重点生产技术难题。这类井由于潜硫量显著增加、压力明显增大,现有络合铁法单井脱硫技术的低硫化氢容量限制了单井脱硫装置撬装化建设,在复杂气质与高压工况条件下存在装置硫磺堵塞与药剂消耗增大等问题,现有技术还不能满足新的生产需求下高含硫单井试采快建快投与长期稳定运行需求。
4.2 天然气净化技术发展趋势
1)脱硫脱碳技术。需持续开发复杂含硫气中多形态硫化物深度脱除技术。目前脱硫脱碳技术多以配方溶剂开发为主,未来发展方向是通过机理研究指导分子结构设计,通过引入功能基团、改变基团之间的结合方式、提高分子活化能等途径,促进目标组分的精准脱除,同时配合工艺和设备优化实现商品气气质提升和净化装置节能降耗。
2)硫磺回收技术。需开展硫磺回收装置检维修期间尾气SO2 减排技术研究,实现天然气净化厂尾气全天候全时段达标。目前已研发并应用了硫磺回收尾气固定床SO2 吸附技术,部分解决了装置开停工期间尾气SO2 达标排放问题。未来发展方向是通过研发高二氧化硫容量可再生SO2 催化吸附技术,实现装置排放尾气自循环处理,杜绝固废二次污染。
3)装置平稳运行技术。需持续研究新开采工艺条件下胺液变质特点和新型脱硫溶剂自身的降解特点及分离特性,持续攻关不同工况下变质胺液复活系列技术,增强对复杂杂质适应性。同时,研发复合材料的无损检测技术、净化装置腐蚀预测技术、净化装置腐蚀风险识别与腐蚀预警技术,综合形成数据传输自动化、风险识别信息化、腐蚀预警智能化的净化厂腐蚀风险管控平台,实现腐蚀管理由被动防腐向主动防腐转变,降低装置腐蚀失效率,延长净化厂检修周期。
4)高含硫气井单井高效低成本净化技术。创新高含硫气井单井净化技术,支撑新发现高含硫气藏单井试采和气井产能快速发挥。针对高含硫气井单井高、潜硫量持续增加的特点,需要提高单井脱硫技术稳定运行硫化氢容量,满足单井脱硫装置橇装化、模块化、小型化建设需求,加快高含硫气井单井撬装化处理装置建设;同时提高单井脱硫技术对中高潜硫量天然气的适应性,降低脱硫过程药剂消耗,实现单井脱硫装置长期稳定高效运行,促进天然气新增产能有效发挥。
5 结论
1)随着中国高含硫天然气开发不断深入,高含硫、高含碳、高含有机硫天然气的净化处理已常态化。高含硫天然气净化过程中的脱硫脱碳、硫磺回收、尾气处理、装置稳定运行等是高含硫天然气开发生产的重要环节,国内“十三五”以来围绕相关工艺和药剂开展了技术攻关,形成了配套技术,取得了显著成效。
2)脱硫脱碳方面,以高含硫天然气有机硫脱除为核心的技术已开发成功并实现工业应用,以CTRedox和CT-LOP 工艺为代表的络合铁法脱硫技术则有力地保障了中国高含硫天然气单井脱硫生产;硫磺回收及尾气处理方面,围绕日益严苛的国家标准要求,研发了大型硫磺回收装置有机硫水解与尾气高效处理技术,实现了装置尾气超低排放;净化装置稳定运行方面,以配方型脱硫胺液复活、高含硫净化厂设备腐蚀防护和装置风险评价为代表的关键技术已全面实现国产化,总体水平与国外相当,部分技术处于国际领先水平。三方面的研究成果为渡口河等高含硫净化厂的建设和运行提供了技术储备。
3)结合中国高含硫天然气开发实际,还需在复杂含硫天然气中多组分有机硫深度脱除、净化装置尾气全天候全时段达标、物理化学类脱硫溶剂复活、高含硫净化厂耐腐蚀材质等方面开展技术攻关,进一步提升中国高含硫天然气开发技术水平。
熊钢, 胡勇, 傅敬强, 等. 高含硫天然气净化技术新进展与发展方向[J]. 天然气工业, 2023, 43(9): 34-48.
XIONG Gang, HU Yong, FU Jingqiang, et al. New progress and development direction of high-sulfur natural gas purification technology[J]. Natural Gas Industry, 2023, 43(9): 34-48.
作者简介:熊钢,1975 年生,高级工程师,硕士;主要从事天然气净化相关技术与管理工作。地址:(610213)四川省成都市天府新区天研路218 号。ORCID: 0000-0002-2721-2850。
E-mail: xiongg@petrochina.com.cn
熊 钢1,2,3,4 胡 勇1,2,4,5 傅敬强1,2,4,5
陈昌介1,2,3,4 杨超越1,2,3,4 颜晓琴1,2,3,4
闫 静1,2,3,4 高 峰1,2,3,4 陈冠杉1,2,3,4
刘其松1,2,3,4 何金龙1,2,3,4 高晓根1,2,3,4
1. 国家能源高含硫气藏开采研发中心
2. 中国石油高含硫气藏开采先导试验基地
3. 中国石油西南油气田公司天然气研究院
4. 国家市场监督重点实验室
(天然气质量控制和能量计量)
5. 中国石油西南油气田公司
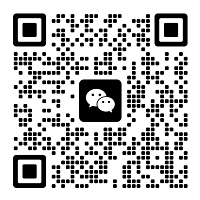
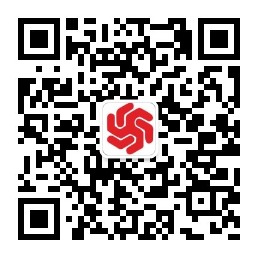
评论