1 模块化橇装化概念
当前发展趋势下,设备集成一体化已经成为石化行业建设工程中新建装置的常规要求,而模块化撬装化组合是重要的集成化方式之一。文章源自云智设计-https://www.cidrg.com/ideabank/wiki/23055.html
文章源自云智设计-https://www.cidrg.com/ideabank/wiki/23055.html
重量超10000吨的模块文章源自云智设计-https://www.cidrg.com/ideabank/wiki/23055.html
撬装化原指一组设备固定在一个角钢或工字钢制成的底座上,通过撬杠或者起重设备就能移动整套装置。工业上撬装设备应用广泛,比如:撬装式发电机组、换热机组、脱水装置等多种形式。文章源自云智设计-https://www.cidrg.com/ideabank/wiki/23055.html
模块化是通过对各种工艺设备的高效集成,使得每个撬块都有独立的功能,同时能够实现不同撬块之间的协同运行,便于分散式搬迁、运移,降低吊装难度。文章源自云智设计-https://www.cidrg.com/ideabank/wiki/23055.html
模块化撬装化设备具有集成度高、设计周期短、施工周期短、占地面积小、控制系统先进、设备噪声小、运行可靠等优点,有效解决了建设现场的施工技术难题。文章源自云智设计-https://www.cidrg.com/ideabank/wiki/23055.html
模块是功能上相对集成,撬块上空间上相对集成,一个模块可能包含几个撬块,一个撬块也可能包含几个模块。文章源自云智设计-https://www.cidrg.com/ideabank/wiki/23055.html
2 模块化撬装化设计文章源自云智设计-https://www.cidrg.com/ideabank/wiki/23055.html
2.1 设计思路文章源自云智设计-https://www.cidrg.com/ideabank/wiki/23055.html
【模块化设计】文章源自云智设计-https://www.cidrg.com/ideabank/wiki/23055.html
①以工艺功能单元为基础,将装置分为多个单一功能单元,形成系列模块单元。
②以模块单元为整体,衡量单个模块单元内设备最大尺寸和重量,同时考量实际运输可行性和现场就位安装便利性,最终将工艺单元模块内的管道、设备、电仪等集成统一整体,确定模块布局。
③模块内的管道设计尽可能包含在模块界区内,阀门宜采用管道直焊,紧凑安装。
④以关键设备为主,配套设备为辅,包括其管线、仪表、阀门全部集成一体,方便后续成撬。
⑤模块单元控制线路、电仪线路均分别提前有序接入装置控制柜,到现场通电后,简单调试确认即可投入使用。
【撬装化设计】
①根据工艺流程,将各模块单元内设备、管道、仪表等全部组装成撬,形成多个单元撬。
②根据设备布置和整体重量情况,确定底座尺寸、承重梁位置和钢结构型号。
③以工艺管道布置图和流程走向在钢结构底座上确定管道支架位置,尽量减少撬间管道连接。
④整体成撬设计时应充分考虑吊装运输、现场安装、方便操作、维修等因素,达到实用性强的要求。
2.2 装置布局要点
以模块化撬装化布置为技术原则,按照划分好的模块单元,设备主要以同一平台布置方式为主,满足间距规范要求,尽可能紧凑摆布,并且满足操作、检维修空间需求。此外,装置内的所有管线、仪表等全部预制安装完成,到现场后,撬间管道焊接碰口即可完成工艺安装。
撬块配管原则撬块配管原则主要有以下几点:
(1)符合工艺流程要求,满足撬块尺寸和重量要求;
(2)便于操作管理,并能保证安全生产;
(3)便于管道的维护和阀门的操作;
(4)要求整体和谐美观,尽量节省材料。
设计人员在撬块建模时应认真遵守配管原则,从设备布置方面下功夫,将相对高的设备布置在中间,相对低矮的设备和阀门布置在撬块周边,如此维修人员及其工具能够很方便地接近设备,对日常运行、维护以及检修、拆装都具有重要意义。如图1所示,脱酸装置中较大的再生塔回流罐布置在撬块中间,两个较小的回流泵及阀门布置在周边。
为了方便将来现场的快速可靠连接,撬块与撬块之间的管道应尽量设计为法兰连接。撬块内如果设置人员通道的话,其宽度不能小于900mm,高度不得低于2150mm。
2.3 设备材料选型要点
设备以工艺需要为依据,满足工艺要求为原则,并尽量体现其技术先进性、生产安全性和经济合理性,以达到标准化设计和工厂化预制。
非标设备的设计依据是工艺专业提供的设备条件表及其附图,设计压力、设计温度应按工艺条件和国家标准《压力容器:GB150.1~150.4-2011》等相关设计标准的规定确定。在设备的设计方面,将根据装置的具体情况,力求做到操作可靠、技术先进、经济合理。
设备尽可能采用模块化撬块化的装备,应考虑采取分段制造、运输,现场组焊、检验,以达到现场模块化施工的效果。
2.4 撬块试压和运输
整个撬块完成设计出图后在工厂进行制造安装,完工后对每一个撬块按照国家标准要求进行探伤、水压试验和气密性试验、吹扫、防腐保温工作,以保证撬块的质量与可靠性,达到出场即能用要求。撬块经历海运和陆运,情况复杂,保证运输过程中撬块不受损伤非常重要。运输时需将设备和撬块分类包装,放置防水箱内,同时为了方便现场布置和拆卸,每个箱子附带清单,写明设备撬块的名称编号、设备清单和图纸编号等。
此外,为了方便清关,所有箱体都要在外面显著处表明项目名称、装置名称、设备标签和采购订单等。
3 模块化撬装化技术的挑战
石化行业模块化撬装化技术将大型装置的生产单元按功能要求和运输限制条件分割成多个单元,分别设计,在预制工厂内对每个模块单元内的设备、管道、仪表等进行预制安装,然后初步整合在一起进行简单调试,再将模块进行拆分,运至现场组装复原,最后经整体调试、试压后运行。这种技术在工程的安全、环保、进度、成本、质量等方面具有显著优势,但在实际应用中也面临一些挑战和障碍。
3.1 技术难题
模块化撬装化技术的实施需要克服一系列技术难题,包括模块化设计的精确性、模块化组件的制造精度、模块化组件的运输和安装的可行性等。
①多专业协同设计:模块化橇装化设备涉及工艺、设备、管道、结构、电气等多个专业,需要高效的协同设计和精确的施工计划。
②三维建模工作量大:由于橇装设备结构复杂,需要进行详细的三维建模以确保设计合理,避免冲突。
③现场组装与拆卸:多层橇装化装置在厂内制作时需分层组装,考虑到现场的吊装、运输和二次组装的需要,需要制定详细的方案。
此外,模块化设计还需要考虑物理条件、资质条件、人和系统条件,以及智能化软件的应用,这些都是实现模块化设计的必要条件。
3.2 标准化和规模化
目前,国内和国际上的模块化设计还处于初步发展阶段,尚未形成标准的、规模化的模块撬装化制造业务链。这意味着在实施模块化撬装化技术时,可能缺乏统一的标准和规范,导致不同项目之间的兼容性和互换性问题。
3.3 环境和安全因素
在某些特殊环境下,如极端天气条件或者复杂地形,模块化撬装化技术的实施可能会面临更多的挑战。例如,在复杂地形油田开发中,需要考虑如何在保证安全的前提下,实现模块化撬装化技术的应用。
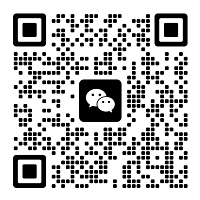
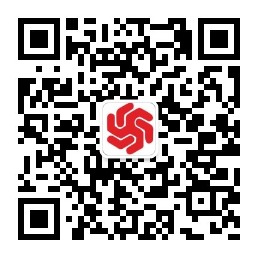
评论